8 Key Elements to Design a High Performance Acoustic Enclosure
June 20, 2017
Overexposure to noise is a constant issue in industrial facilities. To reduce workers’ exposure to noise there are a number of engineered noise control mechanisms available such as control rooms, operator cabins, complete or partial acoustic enclosures, and acoustic walls.
In this article, we will discuss the design and engineering of an acoustic enclosure to enclose a noisy machine or equipment.
What is an acoustic enclosure?
An acoustic enclosure (also known as a soundproof enclosure, sound enclosure or noise enclosure) encloses noisy equipment in a room or a chamber.
For optimal acoustic performance, the exterior of the enclosure must be made with dense and solid material such as galvanized steel whereas the interior must be covered with absorbent material such as acoustic wool. To prevent noise from escaping through the ventilation system, the air inlets and outlets must be fitted with silencers. An enclosure also includes acoustic doors and windows, acoustic tunnels at the entrance and exit of the conveyors and a maximum reduction of openings.
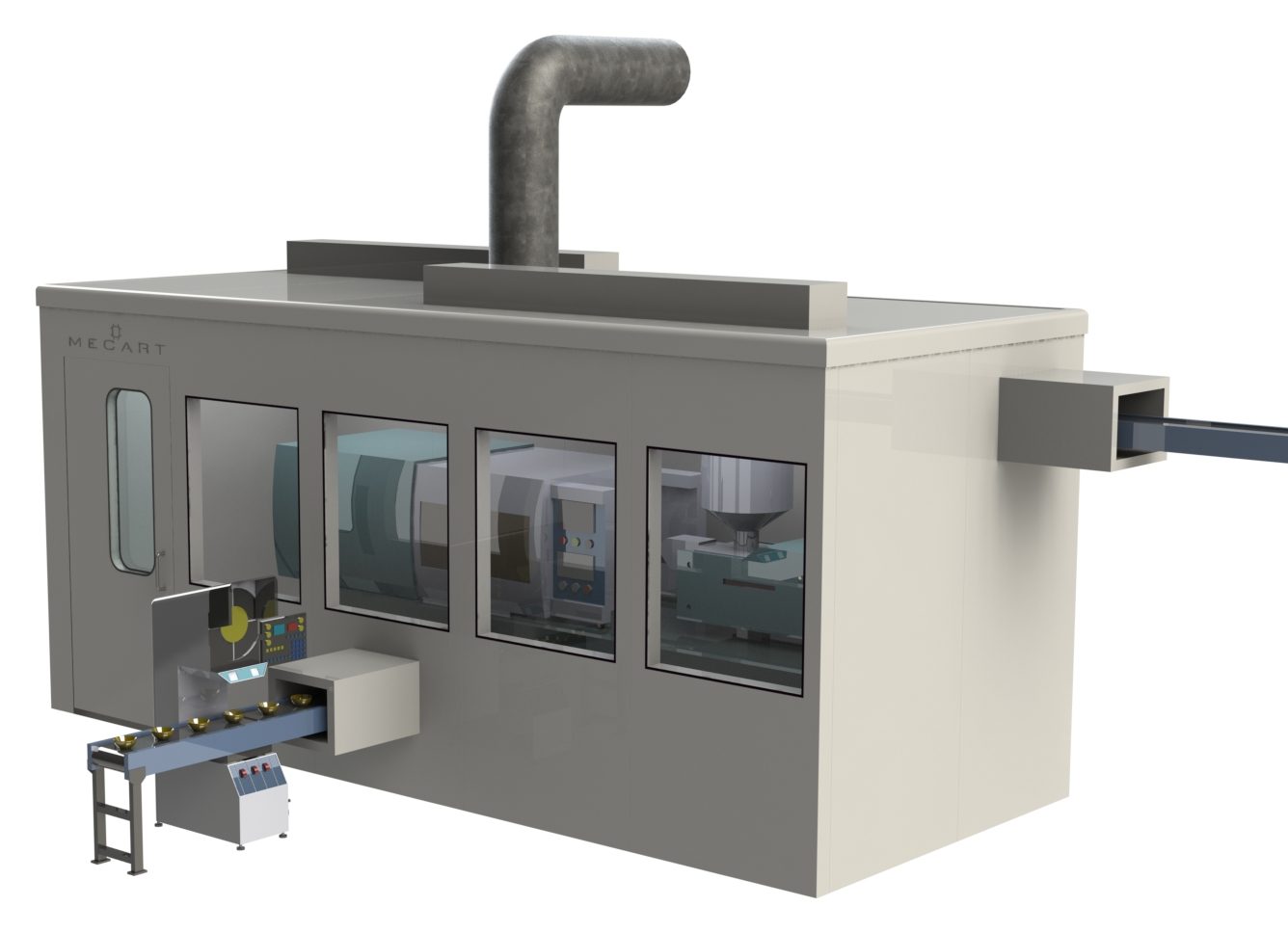
The following 8 questions will help clearly define your needs and make discussions with your noise enclosure manufacturer easier.
#1 What sound reduction are you looking for? (current and desired level)
To calculate a desired soundproofing the sound produced by machinery can be measured with a sound level meter. Ideally, the acoustic enclosure must reduce noise levels below 85 dB (A) (decibel), which is the legal limit in most Canadian provinces. For example, for a machine producing a noise level of 120 dB (A), the sound reduction of the enclosure should be 35 dB (120 dB (A) – 35 dB (A) = 85 dB (A)). This will be referred to as a STC-35 acoustic enclosure. This calculation has been simplified for the purpose of the explanation whereas in reality, the computation is much more complex because the octave bands (high and low-pitched sounds/ high and low frequency) must be taken into account.
The desired level of soundproofing will determine the type of engineering noise control to be chosen. For an acoustic reduction of only 5 to 10 dB an acoustic barrier (one or several walls) will often be sufficient, but for a higher acoustic reduction, a partial or complete enclosure is recommended. A Mecart-brand enclosure with our vibration-dampening system can easily achieve a reduction of 35 to 55 dB. A noise reduction of 70 dB can even be achieved by using multiple-layer walls.
#2 What are the dimensions of the sound enclosure?
The interior and exterior dimensions of the enclosure must be determined. Will the sound enclosure be close to the machinery? Will any operators be working inside? Is it a complete or partial enclosure?
All contact between the machinery and the enclosure must be avoided to maintain the acoustic performance of the enclosure.
If you have space restrictions around the machinery, sliding doors can be a practical solution to allow proper access to equipment.
Where it is not possible to enclose the machinery, a control room, an operator’s cab or any other type of soundproof chamber may be used to isolate the operators from the noise rather than the machinery from the operators.
#3 What are the openings to be expected?
When designing the enclosure, every opening must be thought through and acoustically insulated to prevent noise from escaping the enclosure. Examples of potential penetrations include:
- access for maintenance
- ventilation (fresh air compensation, heat, humidity, condensation)
- utilities, fluids (compressed air, electricity)
- discharge of waste and pollutants (dust, oil mist, gas)
- inlet and outlet for entry and exit of the product
#4 What type of access to the equipment is required? Is access necessary daily or only for major maintenance?
Do you need access to all machinery or only to certain sections? A custom engineered enclosure allows you to design the enclosure according to your specific needs.
The acoustic enclosure can be partially or fully disassembled. Different types of access panels can be engineered for maintenance, from the simple removable panel to the oversized motorized door.
- liftable hood or roof
- Fully liftable enclosure
- oversized doors
- sliding doors
- removable panels
#5 How many doors, windows and removable panels are required? What is their size and where will they be located?
Access restriction to machinery can be a negative side to acoustic enclosures, it is therefore important when designing the enclosure to include the doors, windows and any other access necessary to operate, monitor and maintain machinery.
You may chose all types of doors from a single door to an automatic sliding door. With performant acoustic windows, several options are possible without compromising the acoustic performance of the enclosure.
#6 Do you need ventilation inside the noise enclosure?
The engine and other systems of a machine produce a variable amount of heat. In many cases, the heat must be removed from the enclosure to avoid overheating of the machine.
When designing the ventilation system of an acoustic enclosure, the amount of heat generated inside must be taken into account, including equipment (watt), but also the number of people working inside, computers, lights and any other element producing heat.
In addition, certain types of equipment are very sensitive and require very strict control of temperature and / or humidity inside the enclosure.
The ventilation system may or may not include air conditioning, dehumidification and humidification.
#7 Is lighting required inside the soundproof enclosure?
Depending on the work being carried out inside the enclosure, lighting is sometimes necessary, either to allow the operators to run the machine or to supervise the machinery from the outside. All types of lighting are possible: fluorescent, LED lighting, etc.
#8 Do you need to protect the soundproof enclosure from other elements?
In several plants, noise is not the only harmful element present. The pulp & paper and mining industries are often struggling with high levels of humidity and dust, intense heat, chemical exposure, as well as debris being blown over the enclosure. These hazards can be damaging to buildings that are not resistant enough. The design of a tailor-made acoustic enclosure allows you to adapt the engineering and the choice of materials to the environment of your factory which will increase the sound enclosure longevity to 25 years and more.
It is important to involve operators and equipment maintenance managers when defining the design criteria for the enclosure, as they may raise important factors you may not have thought of.
Do you have a similar issue in your plant?
MECART modular buildings are custom-made to your needs. Our team of experts can find solutions to any challenges your project might be facing. The more difficult the challenge, the more fun we have solving it. Contact us and we will be more than happy to see how we can be of help with your project.